MOPPET Valve
Outstanding Reliability
MOPPET® valves provide outstanding reliability, in even the most demanding service. They deliver consistently longer run times and reduce total life cycle costs. Now, further optimization of the gas flow provides up to 15 percent higher efficiency.
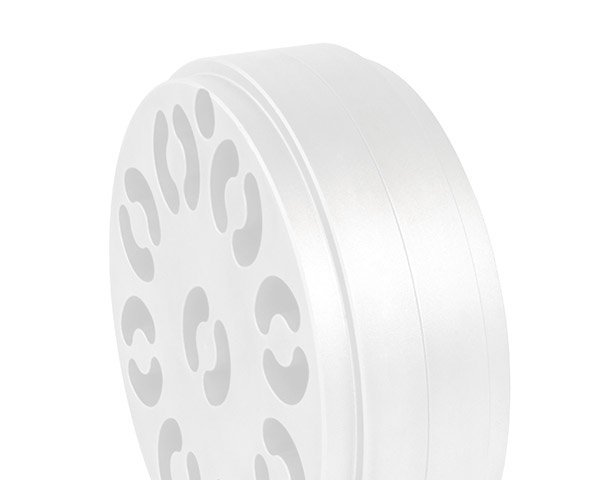
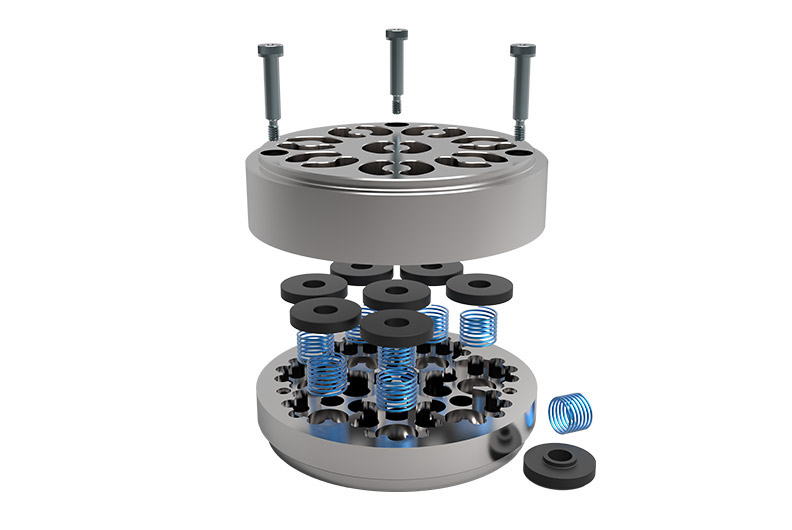
Robust Sealing Elements
A MOPPET valve consists of a series of small, identical sealing elements (discs) that operate independently of each other, helping to disperse liquids and debris and providing outstanding resistance to damage and wear.
Each element is made of durable, lightweight thermoplastic material, which reduces impact inertia. In addition, the thickness of the elements and small center-line diameter make them extremely stiff and resilient to high impact forces caused by extreme pressure, driver speed, or the presence of incompressible matter in the gas.
Maximized Flow
Building on the proven success of the MOPPET valve in severe service environments, Cook Compression has introduced new features to improve efficiency:
- A new smaller MOPPET disc offers more options for configuration and improves flow area in smaller valves
- A new patented disc design optimizes central disc flow
- A milled seat design allows optimization of flow area
- An optimized guard design further increases efficiency
Advanced Spring Design
Springs and spring pockets in MOPPET valves are designed for extended performance in dirty service.
- Spring pockets have generous vent holes that eliminate build-up of incompressible materials that can damage springs
- High lifts and more space between the spring coils allow debris to pass freely through the valve
- Springs have significantly taller free length, allowing for large wire diameter that reduces torsional stress and makes the springs more resistant to damage from debris
Option for Field Repairability
The legacy MOPPET valve design makes field repairs simple and economical. Sealing elements and springs are combined with a seat in a convenient cartridge that can be removed and replaced in minutes with a hydraulic press. Repairs can be performed in the field, with no lapping, grinding or machining required.
Elements and springs are replaced each time a valve is serviced, but cartridges are replaced only when damaged or worn. Incremental replacement reduces costs and helps maximize the utility of each component. MOPPET cartridges are precision-manufactured from 17-4 stainless steel for exceptional corrosion resistance on critical seating surfaces.
The efficiency upgrade of the MOPPET removes the cartridge design to optimize flow area and clearance volume in the valve.
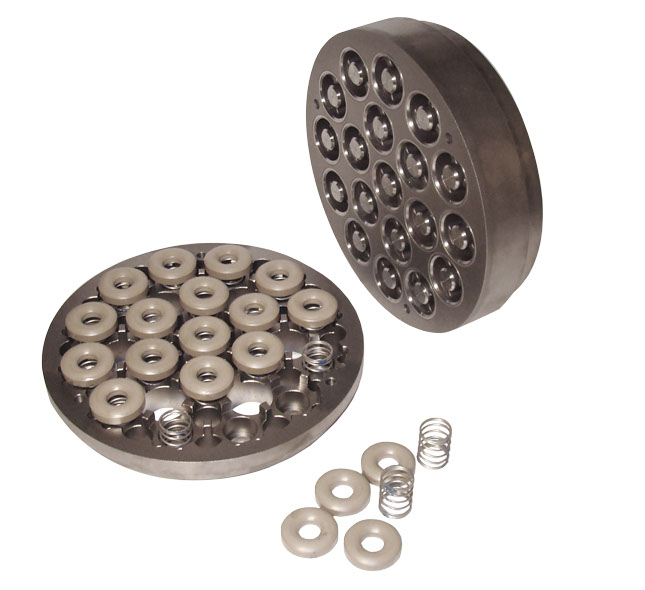
Advantages
- Superior reliability
- Now with up to 15% higher efficiency
- Rugged construction
- Expanded operating range and range of physical sizes
- Interchangeable discs for economical inventory
- Available with finger and plug unloaders
Typical Applications
- Flare gas
- Dirty natural gas
- Hydrogen
- Polypropylene
- Other severe service environments